摘要:基于最近几年发展迅速的可编程计算机控制器(PCC)设计并实现了一种配置灵活、操作方便的水电站监控系统。该系统充分发挥了PCC在通信以及数据处理上的优势,在以极高的可靠性完成机组运行控制、并网控制、保护控制、参数调整等功能的同时,又以其丰富的编程语言以及强大的通信能力实现了机组运行数据统计、模拟量采集以及各种动作记录。该系统为水电站监控系统的设计提供了一条新思路。
关键词:可编程计算机控制器;扫描周期;监控系统;开关量输入模块;模拟量输入模块
0 概述
可编程计算机控制器(Programmble Computer Controller ,简称PCC)是集计算机技术、通信技术、自动控制技术(简称3C 技术)为一体的新型工业控制装置。可编程计算机控制器技术从20 世纪60 年代诞生以来,历经可编程逻辑控制器(Programmble Logic Controller,简称PLC)、可编程控制器(Programmble Controller,简称PC ) ,而可编程计算机均以其极高的可靠性、丰富的编程语言、实用的编程方法、强大的功能、优良的性能、良好的耐恶劣环境的能力成为工业控制领域中增长最迅猛的工业控制设备。随着3C 技术的高速发展,新一代PCC 将逐渐胜任大型集散控制和复杂的过程控制,其良好的兼容性、强大的通信功能、优良的实时性、丰富的功能函数、品种繁多的硬件模块、多种编程语言的使用等,将使PCC 能够适应于各种工业控制的需要。该系统以B&R2005 系列PCC为核心,实现了机组运行控制、并网控制、保护控制、参数自动调整和人工调整、运行数据统计、报警记录、机组温度、机组振动统计、灭磁开关动作统计、事故分闸次数、事故分闸电流统计、发电量分时累计、报表打印等功能。
1 可编程计算机控制器的结构与原理
可编程计算机控制器是一种计算机控制系统,但它比一般的计算机具有更强的为工业自动化控制服务的能力。PCC 系统组成与计算机控制系统的组成十分相似,也具有中央处理器(CPU )、输入/输出(I/O)接口、电源等,如图l 所示。
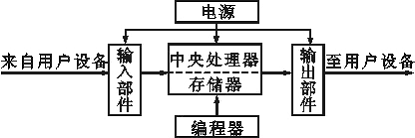
图1 可编程计算机控制器的基本组成
PCC的内核是一个强有力的标准系统元件。由于集成了RISC(精简指令计算机)作为外部通讯,因此可以减轻CPU 的负担。和串口的通讯与主处理器实际操作同时发生,可以避免发生在传统控制系统中的通讯瓶颈问题。
1.l 输入部件
输入部件是PCC与被控对象之间的连接部件,是现场信号进入PCC 的桥梁。PCC 的输入部件均带有光电耦合电路,可以把PCC与外部电路隔离,提高PCC 的抗干扰能力。
1.2 输出部件
输出部件是PCC 与现场设备之间的连接部件,它控制现场设备(如闸门提起、下落、阀门开和关等)。有时为了使PCC 能够直接驱动诸如电磁阀、接触器、灯和音响灯,输出部件通常具有一些大功率器件,例如机械触点式的继电器、无触点的交流开关等。
1.3 中央处理器
CPU 是整个PCC 的核心,它的主要任务为:控制从编程器输入的用户程序和数据的接受与存储;用扫描的方式通过I/0 部件接受现场的状态或数据,并存入输入状态表或数据存储器中;诊断电源、故障和程序中的语法错误等;当PCC 在运行状态时,从存储器读取用户指令,经过命令解释后按照指令规定的任务进行数据传送、逻辑运算或算术运算;根据运算结果,更新有关标志位的状态和输出寄存器表的内容,再经输出部件实现输出控制、制表打印以及数据通信等功能。
1.4 存储器及其扩展
PCC 的存储器用来存储系统和用户的程序与数据。系统程序存储器用来存放系统管理、用户指令解释、标准程序模块、系统调用等程序,常用EPROM (重写只读存储器)构成。用户存储器用来存储用户编制的程序或用户数据。其中,存储用户数据的称为用户数据存储器,常用RAM ,为了防止掉电时信息丢失,采用后备电池作保护。除了上述必不可少的部件,还有通信接口、智能I/0接口、I/0 扩展接口、功能开关与指示灯、编程器等部分。其中编程器的作用是供用户进行程序的编制、调试与监视。编程器有简易型和智能型两种。简易型编程器智能联机编程,并且需要将梯形图转化为其语言后才能输入。智能编程器又称为图形编程器,它可以联机编程,也可以脱机编程,同时具有LCD 或CRT 图形显示功能。PCC 可以采用微机作为编程器,这时微机里应安装有相应的软件包,例如在本系统中,采用微型计算机作为编程器,同时在微型计算机上安装了B&R 公司的软件包Automation SLudio;为了使计算机能够直接与PCC 通讯,计算机上需要有RS232 串口。
2 可编程计算机控制器的工作原理
PCC的工作方式是一个不断循环的顺序扫描过程,每次扫描的时间称之为扫描时间,或者工作周期。典型的扫描周期分为6 个扫描阶段。
2.1 自监视扫描阶段
PCC 内部具有自监视功能,它主要是由监视定时器WDT (Watchdog Timer)完成的,WDT是一个硬件时钟,而自监视过程主要是检查以及复位WDT 。如果复位前,扫描时间超过WDT的设定值,CPU 将停止运行,同时复位输入和输出,并给出报警信号,这种故障成为WDT 故障。WDT 设定的时间一般为150~100 ms ,而一般系统的扫描时间均小于50-60 ms。
2.2 与编程器交换信息的扫描阶段
用户程序通过编程器写入PCC ,以及用编程器进行在线监视和修改时,CPU将总线的控制权交给编程器;当编程器完成处理工作或达到信息交换的规定时间后,CPU 重新得到总线权。
2.3 与数字处理器DPU 交换信息的扫描阶段
当系统配有数字处理器时,一个扫描周期才包含这个阶段。
2.4 与网络进行通讯的扫描阶段
在配有网络的PCC 系统中,PCC 与PCC 之间或PCC 与上位计算机之间在这个阶段进行信息交换。
2.5 用户程序扫描阶段
在这一阶段,根据用户程序存储器所存储的指令,PCC 从输入状态暂存区和其他软元件的状态暂存区中将有关元件的状态读出,并从第一条指令开始顺序执行,每一步的执行结果均存入输出状态暂存区。
2.6 输入/输出(I/O )服务扫描阶段
CPU 在执行用户程序时,使用的输入值不是直接从实际输入端得到的,运算的结果也不是直接送到实际输出端,而是在内存中设置两个暂存区:输入暂存区和输出暂存区。用户程序中所用到的输入值是输入状态暂存区的值,运算结果存放在输出状态暂存区中。PCC 对输入/输出的处理具有以下3 个特点:
( l )输入状态暂存区的数据,取决于服务阶段各实际输入点的通/断状态。当用户程序执行阶段,输入状态暂存区的数据不再随输入的变化而变化。
( 2 )在用户程序执行阶段,输出状态暂存区的内容随程序执行结果不同而随时改变,但输出状态锁存器的内容不变。
( 3 )在输出服务阶段,将用户程序执行阶段的最终结果由输出状态暂存区一起传递到输出状态锁存器。输出端子的状态即由输出状态锁存器决定。
3 系统结构设计
本系统检测和控制的参数主要分为:电量参数、非电量参数以及设备运行、保护状态参数。
3.1 电量参数
包括发电机的三相电压、三相电流、有功功率、无功功率、母线线电压、相电压、直流母线电压等,PCC 与电量仪通过RS485 通讯可以直接从电量仪中读取此上述电量数据;同时机组转速以及频率可以通过与调速器通信读取,也可以通过与转速继电器通信读取。
3.2 非电量参数
包括上导瓦、下导瓦、水导瓦、推力瓦温度,定子铁心温度,冷热风温度,压油罐油压、油位,集油槽油位,漏油槽油位,上下游水位等。其中温度量的采集分别由B&R 2005 系列PCC 的模拟量输入模块和温度巡检仪完成,PCC 通讯模块可以把温度巡检仪采集到的温度量读入PCC 缓存区;辅机系统模拟量例如压油罐油压、油位,集油槽油位等可以由PCC 模拟量输入模块来采集,也可以通过与压油装置的PLC 通信获得;上下游的水位通过PCC 与水位计通信获得。
3.3 设备运行、保护状态参数
包括机组断路器开关、灭磁开关、导叶、进水口闸门、剪断销、水轮机及发电机电气保护开关量状态、事故和故障开关信号状态、油气水三系统工作状态以及励磁系统状态等。这部分状态量可直接引入PCC 开关量输入模块参与机组控制。本系统采用两台工控机作为上位机监控终端,可同时监控三台机组中的任意两台。这两台工控机都必须安装"B&R2005 PVI Manager" ,同时需要在系统中启动"B&R OPC Server"才能实现对同一台机组PCC 数据共享。其中上位机与PCC 站点之间的通信采用抗干扰性能优异的光缆作为硬件连接,数据通过路由器进行中转;软件上则是基于以太网的TCP/IP 协议。
本系统的上位机监控系统采用北京亚控公司开发的组态软件"组态王"进行开发设计。该组态软件能够在PC 机上建立工业控制对象人机接口的一种智能软件包,在该系统中,它以Widows 2000 中文系统作为其操作平台,充分利用了Widows 、系统图形功能完备,界面一致性好,易学易用等特点。该组态软件使得采用PC 开发的系统工程比以往采用专用机开发的工业控制系统更具有通用性,大大减少了开发者的工作量。"组态王"软件包由工程管理器(Proj Manager)、工程浏览器(TouchExplorer)、画面运行系统(TouchView)三部分组成。工程浏览器内嵌画面开发系统即组态王卡发系统。工程浏览器是各自独立的应用程序,均可单独使用,但在工程浏览器的画面开发系统中设计开发的画面应用程序必须在画面运行系统环境中才能运行。
除了上位机监控系统,位于各个机组盘柜上的人机界面也可参与整个系统的监视与现地控制。该人机界面采用HITECH 公司的"ADP6.0"软件包进行开发。
该监控系统框图如图2 所示。
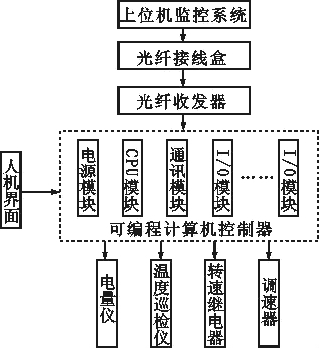
图2监控系统框图
4 结束语
在B&R PCC 系列中,系统总线与I/0 总线是分离的。其中,工业计算机所需要的模块,如附加的处理器模块、远程主站、网络模块等,运行在系统总线上;而数字量和模拟量I/0 模块、定位模块、智能I/0 处理器等则运行在I/0总线上,这样就很好地避免了总线系统的瓶颈问题。I/0总线与系统总线分离,使B&R PCC 系列具有工业计算机能力,而不用添加设备接口(I/0接口),同时系统总线可以进行多处理器操作,这样为了增加工作负载就可以添加多处理器模块。另外,PCC 所有的I/0模块都是电气隔离的,并且采用EMC 方法进行保护,可以有效屏蔽外部干扰,在B&R2005 系统中I/0模块以塑料盒封装,技术人员在安装时可以避免直接与电接触。
本文结合发展迅速的可编程计算机控制器技术,介绍了在水电站监控系统中可编程计算机控制器的应用。PCC(可编程计算机控制器)是整个系统的核心部分,它很好地实现了机组开停机控制、模拟量采集、故障事故报警等功能,同时依靠强大的通讯能力将整个机组原来独立的各个监控站诸如调速器、压油单元、温度巡检仪等连接在一起,并将从这些单元采集到的数据经过处理送到上位机监控系统以及人机界面,比较理想地实现了系统的远程与现地监控。
作者:刘俊(1964,女.湖南桃江人,工程师,从事电力系统通信工作)1,2,许鸿文2 ,殷蔚明2 ,徐汇攀2 ,孔令彬2
l .华中电网有限公司,湖北 武汉430077;2 .中国地质大学机电学院,湖北武汉430074
参考文献:
[l]齐蓉,肖维荣,蔡立虹.可编程计算机控制器教程[M] .西安:西北工业大学出版社,2002 . [2]齐蓉,肖维荣,蔡云虹.可编程计算机控制器高级技术[M] .西安:西北工业大学出版社,2002 .
[3]江秀汉,李萍,薄保中.可编程控制器原理及应用[M] .西安:西安电子科技大学出版社,1998 .
[4]周克良,杨杰,焦海宁.基于现场总线的水电站监控系统设计.中国期刊网:优秀博硕士论文,2004 .