1. 项目简介
蓄电池是工业生产和日常生活中非常重要的电气设备,广泛应用于国防、航空、通信、能源、交通等众多领域。汽车用蓄电池一直是蓄电池市场需求产量最大的品种,随着汽车行业作为国家重点发展支柱产业的飞速发展,车用铅酸蓄电池的用量也迅速增加,大约占整个铅酸蓄电池用量的80%。加之原有汽车对蓄电池的替换需求,汽车蓄电池的市场需求量还将有一个较大的增长。电动自行车作为一种新型代步工具,受到了群众的认可和欢迎,产量和社会拥有量迅速增长,其专用蓄电池的需求量也迅速扩大,产值已超过原来居第二位的固定型蓄电池。目前新能源储能也成为蓄电池新的应用市场,这些新的增长点都为蓄电池行业带来更大的发展空间,而且蓄电池行业的发展,也推动了其他众多行业的发展。
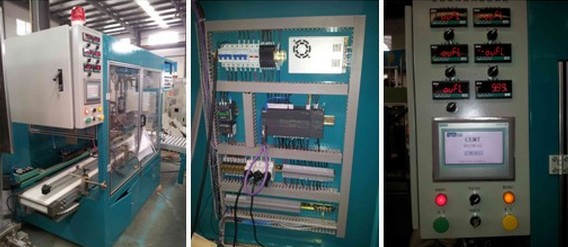
但是,目前蓄电池生产企业众多,竞争也越来越激烈,另外随着汽车行业的逐步开放,外资汽车制造厂在国内逐步发展,导致对配套电池要求提高,这些都要求蓄电池生产企业必须提升产品品质,降低生产成本,来适应新的市场需求。
南京某公司专业生产各种蓄电池专用设备,主要生产极板设备、装配设备、后处理设备、充放电机、检测设备及环保等设备,以良好的质量和较高的性价比,在国内外中高端厂商用户中有较好口碑。
针对市场上对电池生产线检测设备越来越高的要求,该公司推出了全自动短路内阻检测机设备,采用西门子S7-200 SMART PLC 作为主控系统。全自动短路内阻检测机是电池生产线中必不可少的专业质量检测设备,相比以往的设备具有更多的优势。它将以往独立的短路检测机和内阻检测机,融为一体,同时检测短路和内阻,将两个工序并为一个工序处理,缩短处理时间,提高了生产效率,也节约了设备成本。
2.工艺流程介绍
全自动短路内阻检测机是蓄电池质量检测设备,用于将需检测的蓄电池传送到高压短路检测位置和内阻检测位置,分别接通检测电路,进行极板短路检测和焊点内阻检测,以此来检查蓄电池质量。
短路检测采用脉冲高压进行测试,用于检测蓄电池组装过程中正负极板间的安全间距,可靠的检测出极板间存在微短路的电池,快速精确的测试出不合格产品。这样就能在电池组装后,充电之前就检测出错误,获得电池更高的质量产出,大大减少因电池极板短路造成产品的不合格率。
内阻检测用于检查蓄电池穿壁焊接后的焊接质量,给穿壁焊的两个极耳之间加一个恒定的电流,根据穿壁焊两个极耳之间的电阻不同用精密毫伏表测出电压的变化,能够有效的检测电池在穿壁焊过程中出现的气孔、假焊、溅铅等缺陷,从而减小因焊接不达标造成的产品不合格。
全自动短路内阻检测机,通过光电开关检测蓄电池位置,将蓄电池传送到电路和内阻检测位置,下降并夹紧测试机头,自动完成短路检测和内阻检测,判断产品是否合格,执行相应动作。
控制系统流程图如下:见图1
3.方案确定及产品硬件配置
全自动短路内阻检测机,相比以往的检测设备,工艺更加复杂,程序处理量更大,逻辑更加繁琐,且需要与多个设备进行通讯,从而对PLC处理器的性能要求更高。因此,根据其要求最终选择了运算处理速度更快,性价比更高的SIMATIC S7-200 SMART PLC。
本系统使用数字量输入输出点数较多,需要24个数字量输入和22个数字量输出,总共46个数字量IO,选用SR60 CPU模块,其本体集成I/O点数高达60点,充分满足了系统的需求。另外还需要1个模拟量输出,连接恒流源设备,SR60标准型CPU,可方便地扩展模拟量模块,以满足系统要求。
以往的检测设备不带触摸屏,人机交互很不方便,不能实时了解设备运行状态。全自动短路内阻检测机增加了HMI设备,选用了SMART 700 IE触摸屏,使操作更加方便,随时监控设备的正常运行或故障状态。这款7寸宽屏触摸屏相对于上代产品,颜色更加丰富,且集成了以太网接口。S7-200 SMART PLC通过内置以太网接口与SMART 700 IE触摸屏进行通信,组网方便,且通讯快速。
在内阻测试时需使用5个毫伏表、1个电流表,采用MODBUS RTU通讯。通过CPU模块集成485接口与软件集成的MODBUS通讯指令库,很方便地实现MODBUS RTU通讯。(见图2)
主要硬件配置表:
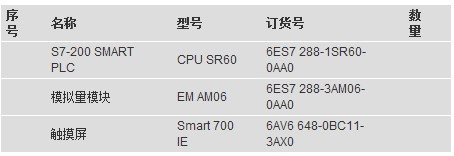
网络配置图:(见图3)
4.软件开发
全自动短路内阻检测机具有手动和自动两种模式。
手动模式可执行滚道启停,高压短路测试机头上升下降,内阻测试机头上升下降,高压短路测试机头夹紧,内阻测试机头夹紧,剔除汽缸开关等手动动作。
自动模式,通过光电开关检测蓄电池位置,使用滚道将蓄电池传送到短路检测位置,自动下降高压短路测试机头并夹紧,接通高压短路测试仪器,短路检测完成后,再将蓄电池传送到内阻检测位置,自动下降内阻测试机头并夹紧,接通内阻测试电路,自动完成内阻检测,并判断电池是否合格,不合格产品通过滚道传送到剔除位置剔除,合格产品传送到下一工序。
模拟量输出连接至内阻测试用恒流源设备,用于设定恒流源大小,信号量程1-5V。通过软件设置模拟量输出通道组态,可选择电流0-20mA或电压正负0-10V,所以必须在程序中进行量程转换,对应1-5V,方可正常使用。
在内阻测试时,需要读取电流表和毫伏表的数值来计算内阻值,这5个毫伏表和1个电流表是通过MODBUS总线与PLC进行通讯的,STEP 7- Micro/WIN SMART 提供便利的MODBUS指令库功能,将子程序转化成指令块,与普通指令块一样,直接拖拽到编程界面就能完成调用。通过设置好相应地址、波特率、读写模式以及数据交换区地址等参数,便可实现PLC与毫伏表和电流表的数据交换。但MODBUS是半双工通讯的,不能同时读写多个设备,所以必须编写轮询程序实现多个设备的数据读写。
5.应用体会
SIMATIC S7-200 SMART PLC集成IO点数更多,性价比更高,更加符合小型OEM设备的需求。PLC本身集成了以太网接口,不需要使用专用编程电缆,使用网线就可以下载程序和进行程序调试,在实际使用中很方便,而且下载速度非常快。
SIMATIC SMART 700 IE触摸屏,颜色更加丰富,显示效果比以前更好。触摸屏本体集成了以太网接口和串口,接口比以前多了,提供了用户更多的通讯连接选择。另外,通过以太网可同时连接3台PLC通讯,相比上一代产品只能与1台PLC通讯,有所增强,可以满足一些特殊应用的场合。
STEP 7- Micro/WIN SMART编程软件,总体上保持STEP 7- Micro/WIN软件界面和功能,改进了一些菜单和窗口,操作方便。移植老程序也很方便,只需复制过来即可。STEP 7- Micro/WIN SMART软件本身集成了MODBUS和USS指令库,不需要另外安装,使用起来很方便。但软件没有集成量程转换的指令库,需要自己编程或从STEP 7- Micro/WIN软件中移植过来,希望以后能够增加集成,从而使编程更加方便。
6.意见与建议
SIMATIC S7-200 SMART PLC只集成了一个以太网接口,在该接口已连接触摸屏,又没有路由器的情况下,想要在线监控程序状态时,需要将触摸屏网线拔下,使用中略有不便。未来是否能考虑增加集成以太网接口,使组网更加方便,也利于程序调试。S7-200 SMART PLC目前没有电池模块,不能满足长时间断电保持时钟和数据的场合,希望能尽早推出电池模块。