摘要:主要介绍了Honeywell公司TPS系统在加氢裂化和制氢联合装置上的应用。介绍了DCS系统的硬件配置,并对一些典型的复杂控制回路的实现和组态进行了说明。
关键字:加氢裂化 制氢 DCS TPS 复杂控制
1、前言
中国石油大港石化公司100万吨/年加氢裂化和4万标立/小时制氢联合装置于2008年一次开车成功。
100万吨/年加氢裂化装置引进UOP公司单段加氢裂化专利技术,详细设计部分由中国石化工程建设公司北京设计院完成。加氢裂化装置采用单反应器双剂串联全循环的加氢裂化工艺,整个装置由反应、分馏、热工和公用工程等部分组成,。主要原料为减压蜡油和焦化蜡油,主要产品为液化石油气、轻石脑油、重石脑油、轻柴油、柴油。
4万标立/小时制氢装置由洛阳石油化工工程公司设计,PSA部分采用成都华西化工公司的变压吸附工艺技术,装置由脱硫、转化中变、锅炉汽包、PSA等部分组成,主要原料为混合干气和天然气,产品为高纯度氢气。
2、系统配置
加氢裂化和制氢联合装置的DCS系统采用了Honeywell公司的TPS系统。TPS(TotalPlant Solution)是Honeywell公司开发的全厂一体化解决方案,TPS把过程控制网络、实时操作网络和工厂信息网络融为一体,是第一个将整个工厂的商业信息系统和生产过程控制系统统一 在一个平台上的自动化系统。TPS具有以下特点:
1)采用可靠的多层的网络架构,实现管控一体化。整个系统由过程控制网络UCN(Universal Control Network)、控制管理网络LCN(Local Control Network)和工厂信息网络组成。
2)系统配置规模弹性大,扩展灵活。TPS系统是一个规模庞大的系统。一条LCN通常距离是300米(同电缆介质),连接40个模件。经过光纤扩展可连接64个模件,最远距离可达4.9公里。一条LCN最多可连接20条UCN,而一条UCN可以连接32台冗余装置,用户可根据需要对LCN上的模件及UCN上的装置及设备进行任意组合,以构成所需要的系统。
3)系统安全可靠、便于维修。系统中的主要硬件设备均采用冗余配置,各模件或设备的故障只影响其自身某些功能,而整个系统仍能继续运行。卡件支持带电插拔,便于设备在线维修。
4)控制功能强大。系统的控制策略非常丰富,包括常规、逻辑、顺控等部分,可以实现从最简单的常规PID控制到先进的复杂的高级优化控制。系统可以通过接口从第三方设备获取数据。
5)系统具有良好的开放性。支持OLE(对象连接与嵌入)技术和ODBC(开发数据库连接)技术。
加氢裂化和制氢联合装置控制系统由一条冗余的LCN(Local Control Network)控制管理网络,两条冗余的UCN(Universal Control Network)过程控制网络构成。LCN网络上共有14个模件 (14个节点),分别是: GUS操作站9台,历史模件HM1台,2对冗余的网络接口模件NIM。LCN网络通过2对冗余的NIM与两条UCN过程控制网络相连接。两条UCN网络:UCN01为加氢裂化装置控制网,包括3对冗余的高级过程管理站HPM;UCN02为制氢装置控制网,包括2对冗余的高级过程管理站HPM。
装置设有一个中心控制室和一个现场机柜室,现场机柜室距中心控制室的距离为260米。控制系统的操作站(现场机柜室工程师站除外)均集中安装在中心控制室内,进行集中操作、控制和管理,LCN网络上的HM、NIM等模件安装在中心控制室的机柜间内。控制系统的控制器(高级过程管理站HPM)安装在现场机柜室。两条UCN网络各用1对500米的冗余UCN电缆连接中心控制室内的NIM和现场机柜室的HPM。在现场机柜室内设有1台工程师站,该工程师站通过1对300米的冗余LCN电缆与中心控制室内的LCN网络连接。
系统配置如下图所示。
图1 加氢裂化和制氢联合装置DCS系统配置图
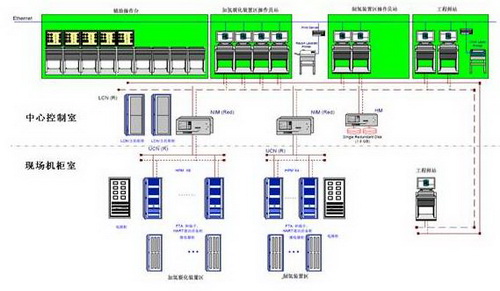
系统共有输入输出信号1186点,具体信号类型及数量见下表
表1 加氢裂化和制氢联合装置DCS系统输入输出信号概况

除上述输入输出信号外,系统还通过485通讯的方式从其他第三方设备中读取相关信号。与DCS系统进行通讯的第三方设备如下:
表2 第三方通讯设备列表

DCS系统通过串口通讯卡件(SI),采用MODBUS协议,通过RS485接口,直接读取上述系统的数据,实现对上述系统的监控。在DCS系统上,通过ARRAY点组态,设置设备地址号、波特率、停止位数、校验方式等。通过通讯接口读取到的所有数据可在控制系统的任意位置获取,并且能在操作员站上显示、报表记录、趋势、报警。
3.主要控制方案
加氢裂化和制氢联合装置的大部分控制回路采用单回路控制和串级控制,同时也用到了很多复杂控制回路。以下主要介绍一下系统中使用的典型复杂控制回路
3.1加氢裂化装置反应进料加热炉温度控制
图2 加氢裂化装置反应进料加热炉温度控制回路
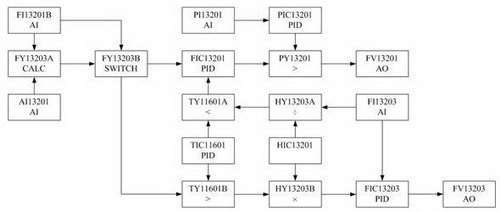
反应器入口温度调节器TIC11601为主调节器,它的输出值是燃料气流量调节器FIC13201及助燃空气调节器FIC13203的给定值。当入口温度偏离给定值时,则温度调节器TIC11601的输出值发生变化,即燃料气流量调节器FIC13201及助燃空气调节器FIC13203的给定值变化,因此调节器FIC13201/13203的输出改变,燃料气调节阀FV13201和助燃空气调节阀FV13203的开度相应变化,进入炉子燃料气和助燃空气流量变化,使反应器入口温度达到给定值。
助燃空气流量的远程设定点,是通过信号选择器选择的加热炉出口控制器TIC11601输出信号,或是来自选择开关FY13201B(该选择开关有两个流量供选择,一个是通过密度和线性流量计算出来的补偿质量流量,另外一个就是由FI13201B输送的线性流量)的燃料流量信号,通过高信号选择器TY11601B选择流量大的,高信号选择器的输出乘上空气/燃料比(来自HIC13203)设定值,再乘上空气质量/燃料质量理想配比的默认比值15.5,为助燃空气流量控制器FIC13203提供远程输入,按要求来调节助燃空气的流量。助燃空气流量信号作为除法器HY13203A的输入,除以空气/燃料比(HIC13203)设定值,再除以空气质量/燃料质量理想配比的默认比值15.5,获得允许的燃料气流量信号,作为燃料气低选器TY11601A的一个输入信号。低选器的另外一个输入信号来自炉出口温度控制器TIC11601的输出信号,通过低选器选择较小的信号,作为燃料气流量控制器FIC13201的设定,通过控制器来控制调节阀FV13201,从而实现燃料气流量的调节。另外在燃料气的流量控制阀前还有一个高信号选择器PY13201,该选择器对来自于流量控制器FIC13201和加热炉火嘴压力控制器PIC13201进行高选后输给流量控制阀FV-13201。这样的控制可有效抑制燃料气的调节延时。
该控制回路的控制理念是,低温信号先增加助燃空气再增加燃料气,高温信号先减少燃料气再减少助燃空气,目的就是通过助燃空气来限制燃料流量的增加,提高燃料气的利用效率,节约燃料气。
3.2加氢裂化装置总进料换热器混氢流量均分控制
图3 加氢裂化装置总进料换热器混氢流量均分控制回路
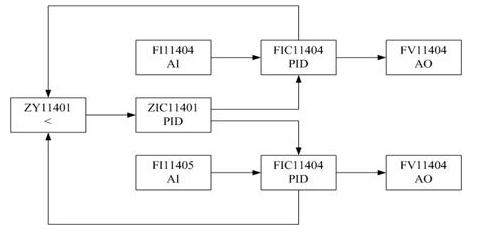
总进料换热器采用的是两个换热器并联的方式,这样可以提高换热器的换热效率,两股冷进料混合氢和混合原料油均采用了严格的流量均分控制,主要是为了使加热炉的两路进料得到均分,以此防止加热炉的炉管因流量不均导致结焦和炉管故障。混合油的流量均分控制主要是通过两个流量控制器进行均流量给定来实现的。混合氢的流量均分控制是通过使一个调节阀处在几乎全开的位置,而使另外一个调节阀工作在截流位置来实现的。两路混氢各设一个流量控制器,每个流量控制器的输出信号,受低选器ZY11401的监控,低信号通过选择器,用作均衡控制器ZIC11401的测量信号,通常把ZIC的设定点设定在10%左右,以保持系统中的一个调节阀(FO)处在几乎全开的位置,控制器输出给两个流量控制器来根据各路阻力调节阀门开度,从而实现流量的均分控制。
3.3加氢裂化装置新氢压缩机一段吸入罐压力控制
图4 加氢裂化装置新氢压缩机一段吸入罐压力控制回路
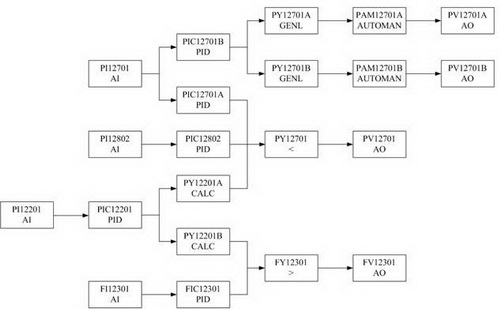
新氢压缩机一段吸入罐通过一个压力的分程控制(PIC12701B)来实现压力高的控制,压力低是由新氢出口返回线来实现控制。当冷高压分离器压力下降,压力控制器PIC12201输出在0~50%内时,经反向转换100~0%进入低选PY12701,当选上时由PIC12201回路控制返回线阀门PV12701(FO),使PV12701开度变小,返回量减少,进入反应系统的氢气量增加,使冷分离器压力上升到给定值。当高分压力下降时,新氢压缩机三级出口返回量少,给系统补充量多,此时新氢入口分液罐压力下降, PIC12701A正作用输出进入低选PY12701,当新氢入口分液罐压力很低时,会被低选器选上,所以由PIC12701A控制返回线阀门PV12701,保证压缩机的压力达到稳定值。低选器PY12701的另一路输入为新氢机出口压力控制器(PIC12802)。当高分压力上升,PIC12201输出在50~100%时,经转换为0~100%去作用阀门FV12301(FC),即去冷闪蒸尾气线。
3.4制氢装置转化炉水碳比控制
图5 制氢装置转化炉水碳比控制回路

进转化炉水蒸汽和脱硫后原料气流量进行水碳比的比值控制是制氢装置最重要的控制回路,控制好水蒸汽与原料气的水碳比是转化操作的关键。一般情况下正常的水碳比值为3.5:1,水碳比过高,不仅浪费水蒸汽,而且增加转化炉的热负荷;水碳比过低,会引起催化剂积碳,使催化剂失活,甚至造成生产事故。该控制回路是通过测量脱硫后原料气的流量,计算出原料中的碳含量,由比例器根据碳含量按比例计算出所需要的水蒸气的流量,进行比例控制。
3.5制氢装置锅炉汽包液位控制
图6 制氢装置锅炉汽包液位控制回路
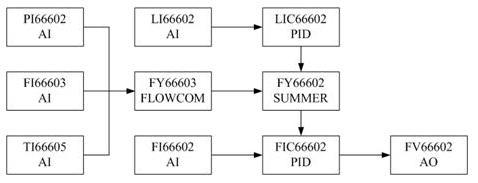
锅炉汽包的液位控制采用三冲量控制,即汽包进水量,汽包的饱和蒸汽量,汽包液位,三个参数经过计算后,通过控制汽包进水控制阀来控制汽包液位。汽包液位是主控变量,引入蒸汽流量信号,是为了及时克服蒸汽流量波动对汽包液位的影响,并有效地“假液位”现象引起控制系统的误动作;引入给水流量信号的目的是将给水流量信号作为副变量,利用串级控制系统中副回路克服干扰快速性来及时地克服给水压力变化对汽包液位的影响。该控制回路中,FY66603是蒸汽流量的温压补偿模块,FY66602是计算模块,计算表达式为:OUT=FY66603.PV+C2*(LIC6602.OP-50)/100(C2为给水流量的量程),计算结果作为给水流量调节器FIC66602的给定,组态时该模块使用了Regulartory Control中的Summer算法,当给水流量调节器不处于串级模式时,液位调节器LIC6602的输出会跟踪表达式50+100*(FIC66602.SP-FY66603.PV)/C2的计算结果,从而可以实现操作模式的无扰动切换。
4.结束语
控制系统投用至今,运行状况一直正常稳定,各控制回路控制效果良好,能实现生产工艺的控制要求。