关键字:实时数据库 化工 能源管理 生产信息
一、应用背景
在现代的化工生产企业中,对生产车间的生产装置工艺进行实时的数据采集和保存,可以为生产工艺过程的跟踪、分析、评价、操作优化、事故原因
的分析查找,提供最直观的数据,通过数据的分析,不断的科学性优化管理,为了提供工厂的利润率,带来了必要的保证。
二、用户需求
通过集成企业实时数据库系统,实时采集生产过程装置数据,实现网络化的生产监视。
- 根据 DCS 的配置情况,自动采集生产过程数据到实时数据库。
- 建立生产实时数据库系统,存储工厂实时、历史信息,如:生产装置过程数据、配电数据等。
- 通过建立虚拟计算点,以方便地实现对所关心的主要生产装置的产量、收率、能耗等实时计算。
- 能够自动读入人工录入数据。数据经过处理和组织能用图形、报表等方式形象直观地表示出来。
三、现场概述
系统采集的数据主要有两方面的来源:
1、通过标准 OPC 接口采集 DCS 系统的数据;
2、通过 RS-485 串口采集智能电表的数据(大概 170 左右个电表);
系统需要实现如下三个核心功能:
1、现场实时数据的汇总存储;
2、现场实时数据的动态展现;
3、相关统计报表的生成;
四、系统框架
在本系统中,紫金桥实时数据库起到了数据采集、处理和发布的一个核心位置,整个系统框架如下:
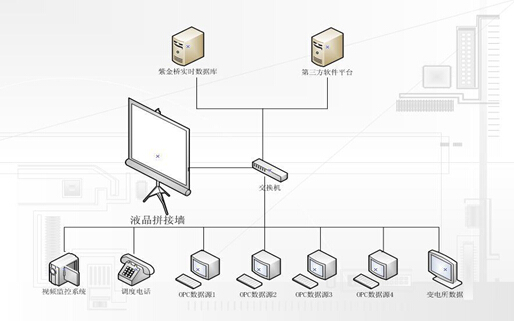
在本系统中,紫金桥实时数据库将现场的多个OPC数据源以及变电所的电力数据通过以太网的形式采集过来,然后进行数据的压缩保存、同时对生产工艺的流程图进行动画的演示,再接下来将处理过后的画面通过IIS的方式发布出去,最后由第三方软件平台将紫金桥 实时数据库发布的数据与视频监控系统等一起整合,投放到液晶大屏上。
五、系统功能
紫金桥实时数据库在本系统中应用:
1、根据底层设备提供的OPC接口,通过以太网的方式将OPC的数据进行采集;
2、针对采集点的分类,对故障报警的点进行历史记录、实时报警,对采集的大批量连续工艺数据进行高效的压缩;
3、通过ODBC的方式将关系数据库的数据进行操作;
4、通过IIS的方式将工程画面进行WEB发布;
5、各种工艺流程的动画显示;
6、关键工艺参数的实时监控;
7、各种 PLC、智能仪表等设备的预留接口。
具体实现如下:
生产装置流程监视:
包括分装置分单元的工艺流程图监视,基本与DCS流程图一致,包括装置、物流、设备号、位号、单位、实时数据和关键点动态曲线等信息的显示。
关键参数集中监视:
根据工艺要求,将整套装置或所有装置的关键工艺参数点,例如环境检测点、主要温度、流量、压力、液位、质量、计算统计点、能耗绩效指标、产量指标、负荷等集中在一张报表和流程图上显示。
有毒有害气体及环保数据监视:
根据安全要求,将整套装置或所有装置的有毒有害气体报警信号及环保相关参数点等集中在一张报表和流程图上显示,并提供相关的报警显示功能,招标方提供相关系统的数据接口及通信协议。系统预警方式:PC 电脑、手机短信。
生产装置总貌监视:
根据企业的装置总貌图,配以关键位号,实现通过监视一幅流程图即可了解装置或全公司生产全貌的功能。
储罐集中监视:
根据罐区分布和检测数据,将内部重点防范区域的储罐罐存 量、温度、压力、周围可燃气体检测等信息的集中监视画面,便于安全、环保和生产管理人员对罐区的实时掌控。
能源管理:
a) 能耗动态监控
在能源管理模块中可以实现实时对企业的能耗进行计算及分析,对特殊重要的能源数据进行统计分析,以曲线或柱状图的方式实现对比分析。包括装置各介质实时能耗比重、装置各介质实时能耗趋势和装置实时综合能耗趋势。
在能源管理中,根据能源消耗模型可以实现快速的能源消耗计算和分析,依据能源介质创建不同的动态监控页面,实时计算分析能源消耗数据,包括装置各介质能耗数据,装置各能源介质能耗比重,并由此得
到装置各能源介质实时能源消耗变化趋势、装置实时综合能耗趋势等。
b) 能耗统计分析与展现
能耗数据计算
在能源管理中,系统可以自动(或手动)快速计算能源消耗数据,后台服务进程或客户端程序可以依据职能划定的不同,依据能源消耗模型以及能耗统计计算公式,定时快速计算获取能耗数据,如:装置、单元的日/月能耗数据,厂、装置、单元的日/月能耗消耗数据。
能源报表系统
针对每个能耗装置、能耗考核单元,基于计算获得的能源消耗数据,自动生成能源报表,以便直观地展现各装置、各单元的当前能耗状况,能耗报表包括:车间能源消耗报表
1、能源完成情况表
2、装置各介质能耗统计报表
3、工业企业能源消费统计表
4、生产厂能耗报表
能耗分析
基于计算获取的能源消耗数据,可以对能源消耗情况进行分析评价,能源消耗数据全部存储在数据库中,对生产装置能耗现状和趋势进行分析。
装置的物料流量 趋势根据装置实际物料进出情况,开发一套集中监视原料和产品趋势图,使得工艺人员可以更加直观的进行物料流量的监控、生产历史分析。
六、系统应用效果图
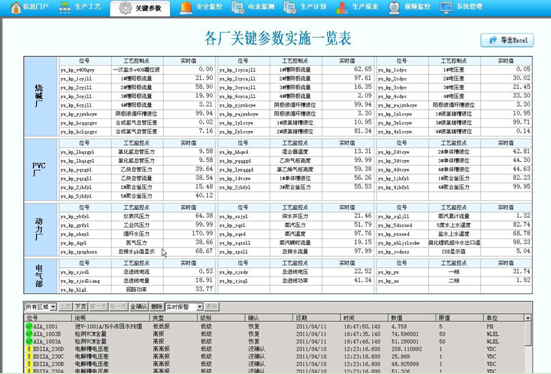
